球墨铸铁管工艺流程——退火炉工段篇
退火工段在球墨铸铁管的生产过程中负责球墨铸铁管的退火处理。
成型铸管送入退火炉——炉内退火——完成退火出炉
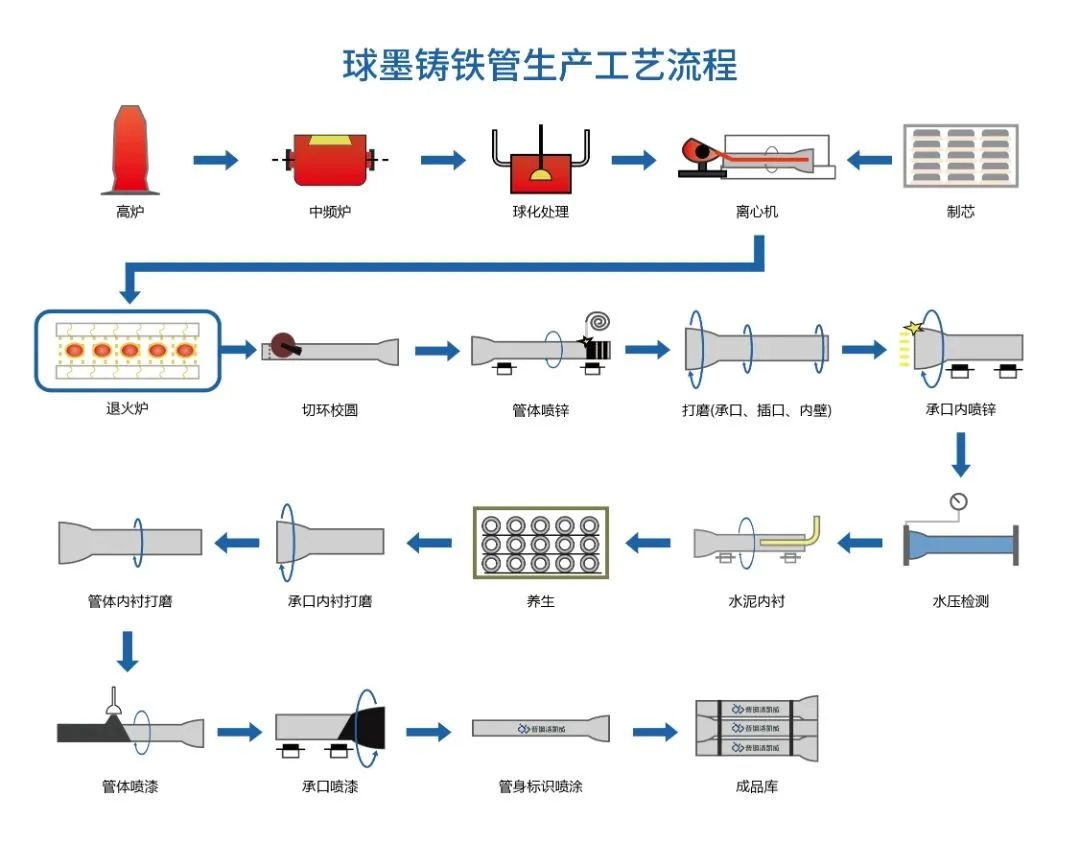
1.送管链条上进行人工扒砂(砂芯残余)。
2.吹砂机将球墨铸铁管内的散砂吹出。
3.送入退火炉进行退火热处理。
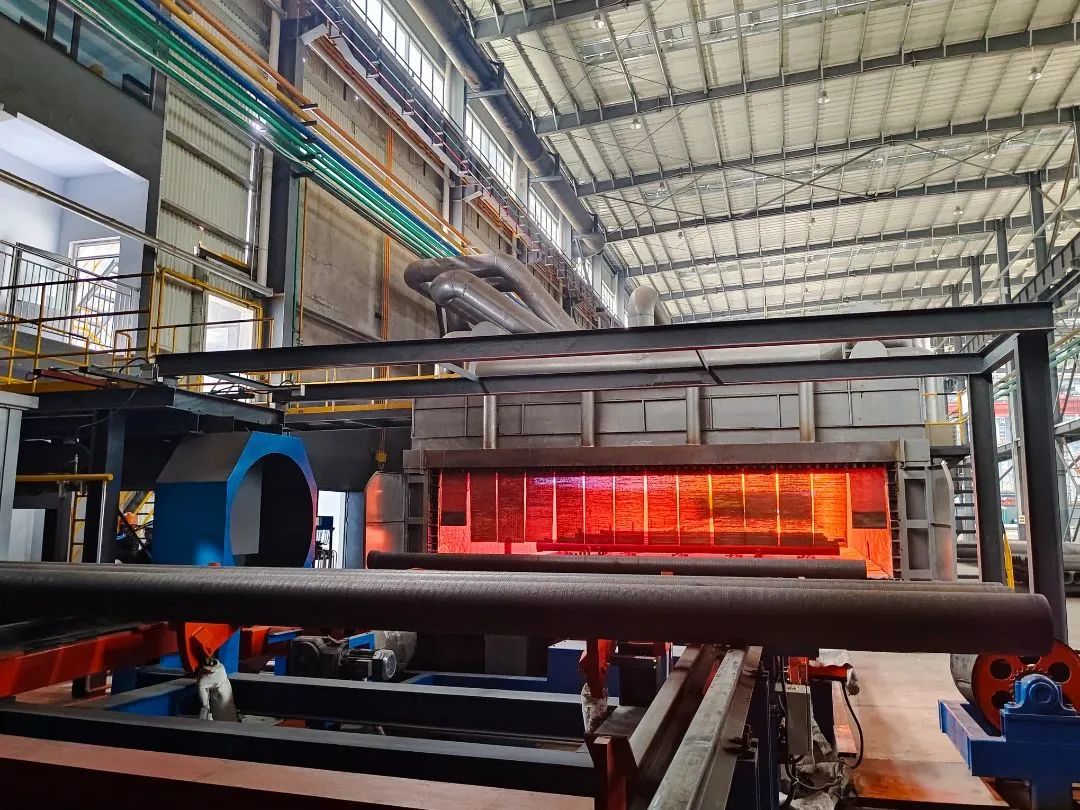
球墨铸铁管的具体退火温度及保温时间是由不同的化学成分和铸态组织所决定的,对不同生产工艺条件的铸管,其退火工艺是不同的,由试验决定。
铸管生产厂的退火工艺共分为五段(加热1段、加热2段、保温段、急冷段、缓冷段),要求共晶渗碳体在保温段全部得到分解,进入缓冷段后,珠光体开始分解。
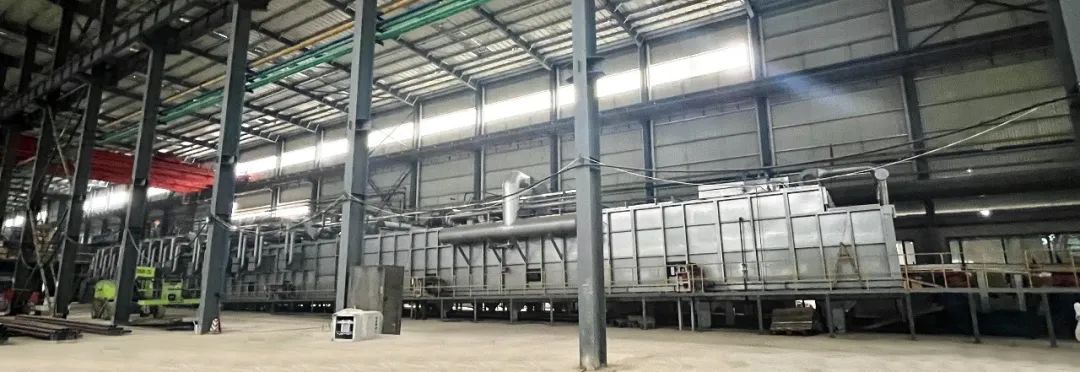
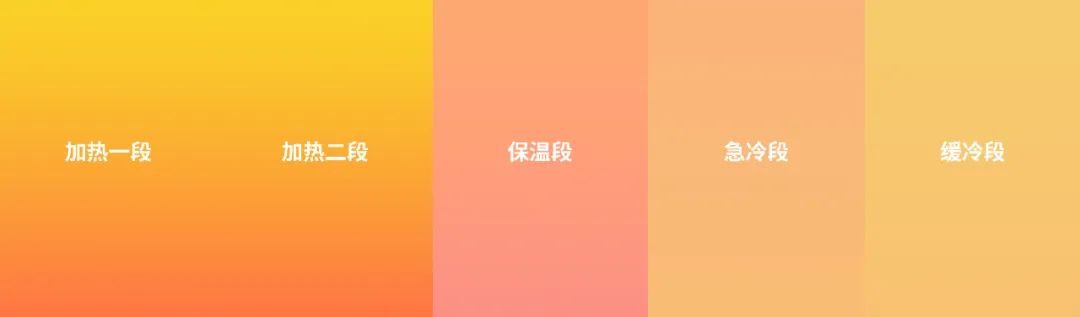
低温退火原理:
将铸件加热到设定温度,保温一定时间,然后随炉缓冷至设定温度出炉空冷,使珠光体中渗碳体发生石墨化分解(珠光体是渗碳体和铁素体的混合物)。当铸态球墨铸铁组织中只有铁素体、珠光体及球状石墨,无自由渗碳体时,为了获得高韧性的铁素体球墨铸铁,可采用低温退火。
球墨铸铁的力学性能主要取决于金属基体,通过热处理控制奥氏体化温度、保温时间和冷却条件,可以改变奥氏体及其转变产物碳的质量分数,从而可以显著改善球墨铸铁的力学性能。在热处理过程中,石墨作为球墨铸铁中的一个相,也参与相变过程。石墨的存在相当于一个储碳库,形成铁素体球墨铸铁时,碳全部或大部分集中于石墨这个储碳库中。球墨铸铁热处理加热时,球状石墨表面的碳有部分溶入奥氏体,供应必要的碳量。
1.完成退火的球墨铸铁管经运管链条运送至切环工作台进行切环取样。
2.抽检的样品被送入金相检验室进行检测。
3.确认样品金相、性能达到国家标准后进入后线工序。

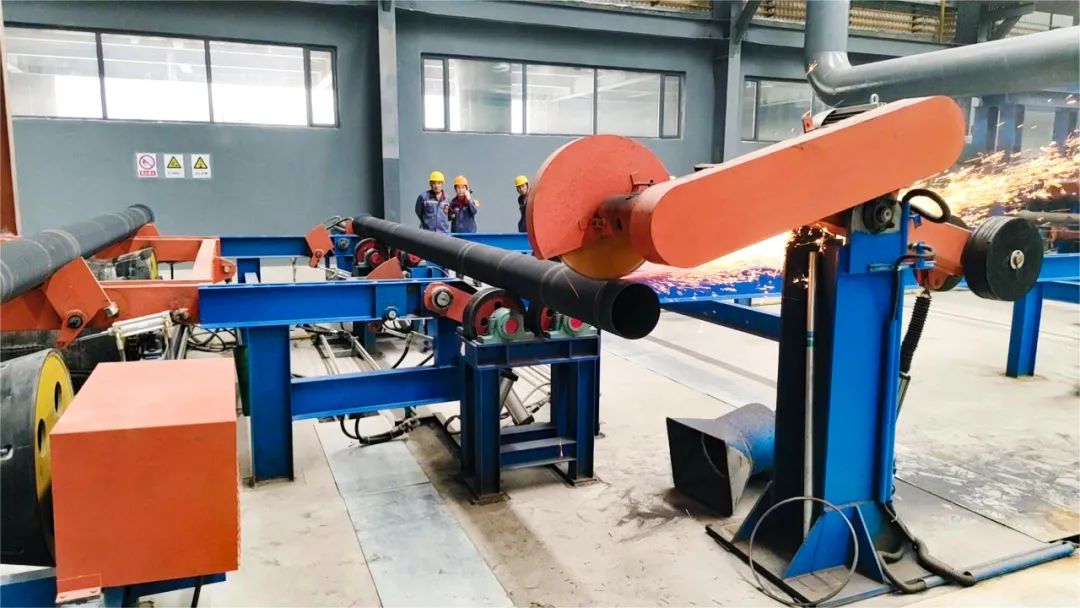
DN80—DN600的球墨铸铁管:
≤15%珠光体、渗碳体≤3%
DN700—DN1000的球墨铸铁管:
≤20%珠光体、渗碳体≤3%
DN1100—DN2000的球墨铸铁管:
内中外壁平均值
请先 登录后发表评论 ~